Kupol Project collabora con Sculpteo e sfrutta la tecnologia HP Multi Jet Fusion per reinventare il casco sportivo
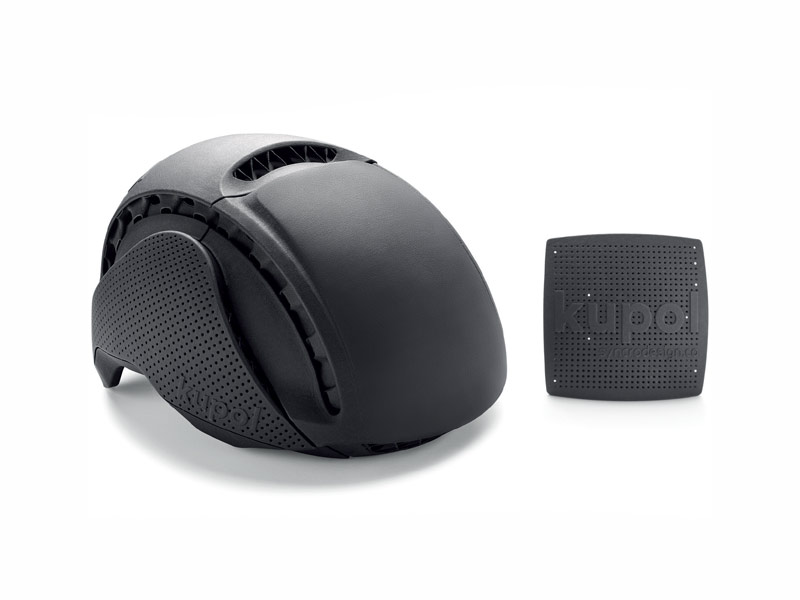
Un ufficio servizi e un cliente si avvantaggiano reciprocamente con la tecnologia di stampa 3D di HP
Syncro Innovation è una società di design industriale situata in Quebec, in Canada. Utilizzando la produzione additiva, collaborano con i clienti per dare vita a nuovi prodotti innovativi. Il team di Synchro risolve i problemi, andando dove l’innovazione li guida. Si concentrano principalmente sul settore degli articoli sportivi e hanno sviluppato, tra gli altri prodotti, tipi unici di caschi da bicicletta, racchette da neve e borracce.
Nell’ultimo anno, l’amministratore delegato di Synchro, Gabriel Boutin ha iniziato a esplorare i modi in cui la stampa 3D potrebbe essere utilizzata per reinventare il modo in cui i caschi sono realizzati. I suoi sforzi hanno portato a una svolta significativa, che è diventata il progetto Kupol.
Per aiutarlo nei suoi sforzi, Gabriel contattò Sculpteo e iniziò a lavorare con loro per sviluppare il suo nuovo prodotto. Sculpteo è una società leader nella produzione digitale e fornisce servizi di stampa 3D professionale e taglio laser per la produzione su richiesta di prototipi, oltre alla produzione a breve termine di prodotti per uso finale.
Sfida
“Ho progettato caschi da bicicletta per oltre sette anni“, afferma Gabriel Boutin, direttore del progetto Kupol. “Ci sono stati molti limiti nella fabbricazione in serie e soprattutto quando si utilizza la tradizionale schiuma di polistirene espanso (EPS) per l’interno del casco. Il mio ruolo di designer è quello di ripensare i prodotti in meglio. Volevo creare un casco più leggero e più funzionale“, afferma il direttore del progetto Kupol, Gabriel Boutin.
I caschi da bicicletta sono tradizionalmente fabbricati in due pezzi. L’esterno è realizzato in plastica stampata ad iniezione. L’interno è realizzato in schiuma EPS, quindi i due vengono combinati per formare il prodotto finale.
Poiché si basano su metodi di fabbricazione in serie, la prima grande sfida è che entrambe le tecnologie richiedono un impegno per volumi elevati. Oltre a creare costi iniziali significativi, ciò limita anche le opportunità di personalizzazione. Inoltre, la schiuma EPS respinge l’umidità e intrappola il calore sulla testa del guidatore. Sebbene i caschi moderni includano slot di raffreddamento per aiutare a mitigare questo problema, non lo eliminano completamente.
Soluzione
“Sono stato nel mondo della stampa 3D per 15 anni“, afferma Boutin. “È sempre stato importante per la nostra azienda. Ma fino a poco tempo fa la tecnologia non era abbastanza veloce e i materiali non erano abbastanza forti per questa particolare applicazione. Quando HP ha introdotto la sua nuova tecnologia Multi Jet Fusion, ero entusiasta di provarlo. Se fosse stato in grado di soddisfare le nostre esigenze e mantenere i costi in linea, avremmo avuto una significativa opportunità di reinventare un elemento chiave nel ciclismo“, afferma il CEO di Sculpteo, Clement Moreau.
Boutin ha iniziato creando un nuovo design del casco che eliminasse la necessità di schiuma EPS. Ha creato una struttura aperta all’interno del guscio dell’elmetto che avrebbe consentito la personalizzazione, migliorando al contempo la traspirabilità.
Ha contattato il team di Sculpteo e ha chiesto loro di creare un prototipo. La prima generazione non è stata progettata per resistere agli urti, ma nel corso dell’anno successivo hanno continuato a perfezionare il modello. Insieme, Kupol e Sculpteo hanno creato diverse versioni e quelle sono state testate per la resistenza agli urti, tra gli altri fattori. Dato il gran numero di prototipi creati, anche la velocità era di fondamentale importanza.
Prima di lavorare con la tecnologia HP, Boutin aveva provato altri metodi di stampa 3D, tra cui FDM, SLA e SLS, ma erano molto lenti e nessuno era in grado di fornire la resistenza anisotropica di cui aveva bisogno, soprattutto considerando le pareti sottili che doveva usare nel suo design. Inoltre, la finitura superficiale e la minore porosità di Multi Jet Fusion gli hanno permesso di creare un design attraente dal punto di vista commerciale.
Una volta completati i test, il progetto Kupol aveva finalmente un prodotto pronto per essere immesso sul mercato.